Operations Plant Director
Job
Overview
United States Sun Valley
- Engineering and Project Management
- Permanent
You are subscribed to our push notifications, but not currently for jobs like this.
Would you like to receive notifications for jobs like this as well?
Great news! You are subscribed to receive alerts for jobs similar to this one.
This vacancy has now expired. Please see similar roles below...
We currently seek a high caliber Operations Plant Director for a long-term basis within our client’s team of experienced professionals. Based in Sun Valley, CA.
Job Requirements:
- Ensures production performance to meet safety, quality, cost, and technology standards to fill customers’ needs while maximizing productivity standards.
- Schedules human and technical resources to produce to plan within all budgetary limitations.
- Takes leadership role in implementation and maintenance programs.
- Participates in the hiring, orientation, and training for new production employees.
- Provides leadership and takes initiative to ensure all processes, activities and use of equipment is performed within a safe, clean, and organized environment.
- Be constantly aware of the process/workplace safety. Notify management to potential issues or shortcomings and provide solutions that are process friendly, cost effective and protect our employees.
- Responsible to ensure all production data input is transacted accurately and timely.
- Coordinates with other departmental managers to ensure operations are following all regulatory and statutory requirements.
- Creates an environment which supports teamwork and group participation; develops, coordinates, and motivates departmental inter-organizational teams.
- Assess employee skills and performance to identify training and remedial development needs; invests in employee career development through training and work assignments; assists the Plant Manager in decisions on staff promotions.
- Is a readily available resource and takes the leadership to solve production problems that impact safety, quality, output, resources, costs, and product availability.
- Under the direction of the Plant Manager, coordinates scheduling and activities for new product development, special projects, and plant upgrades to meet scheduled timelines.
- Provide support to improve process, and/or products.
- Support plant management and maintenance in the selection of proper components, engineered materials, and wear parts for maximum effectiveness and optimal cost.
- Be constantly aware of the process/workplace safety. Provide solutions to any and all discoveries of potential hazards and ensure the safety of our employees.
- Identify, resource and work with outside vendors as required.
- All other duties as requested or assigned.
Qualifications:
Technical Skills & Knowledge
- Strong mechanical, electrical, and technical skills
- Knowledge of mechanical handling, conveying, hydraulic, pneumatic, mixing, curing, and packing equipment
- Critical thinking and problem-solving skills; demonstrated leadership skills
- Knowledge of basic OSHA regulations within a manufacturing/distribution environment
- Excellent interpersonal, written and communication skills; detail oriented
- Receptive and responsive to innovative ideas and suggestions
- Develop strategies, set priorities, and maps a course of action to achieve objectives
- Ability to lead, motivate, persuade, inspire, and build trust, consensus, and teamwork
- Good computer skills: Microsoft Office including Excel, word; manufacturing software, and AutoCAD is a plus.
- Minimum Bachelor’s Degree in Mechanical or Industrial Engineering
- Bilingual is a plus
- A minimum of 5-8 years experience in a manufacturing environment;
- Knowledge of concrete products desirable
- General Manufacturing environment with a hands-on approach
- Standing, walking on the factory floor much of the day
- Lifting heavy materials, 70 pounds maximum
- Organize and schedule work effectively
- Adaptive to change in a fast-paced environment with sometimes critical deadlines
- Work under pressure with quick priority changes
- Handle multiple tasks
- Work independently as needed
- Provide mentoring, problem solving, intervention, team building, motivating
- General manufacturing environment
***Notice to Candidates: Background checks are carried out as part of any conditional offer made, including (but not limited to & role dependent) education, professional registration, employment, references, passport verifications and Global Watchlist screening.
To be Considered Candidates: Must be authorized to work in the USA without sponsorship***
Employment Type: Direct Hire
Location of Position: Sun Valley, CA
Location Type: On-Site
Pay range: $100K - $140K
“We are an equal opportunity employer that recognizes the value of a diverse workforce. All qualified individuals will receive consideration for employment without regard to race, color, age, sex, sexual orientation, gender identity, religion, national origin, disability, or any other criteria protected by governing law.”
We are an equal opportunity employer that recognizes the value of a diverse workforce. All qualified individuals will receive consideration for employment without regard to race, color, age, sex, sexual orientation, gender identity, religion, national origin, disability, veteran status, genetic information, or any other criteria protected by governing law.
Sign-up for Job Alerts
Our latest jobs
Negotiable
United Kingdom, , Flintshire
$ 60 Per Hour
United States, Augusta, Georgia
Negotiable
United States, Ladson, South Carolina
Negotiable
United States, seneca, South Carolina
Negotiable
United States, East Hanover, New Jersey
$ 120000 - $ 130000
United States, Ridgeville, South Carolina
Negotiable
Poland, Nysa, Opolskie
Negotiable
United States, Houston, Texas
Negotiable
Poland, Nysa , Opolskie
Negotiable
Poland, Nysa , Opolskie
Our insights
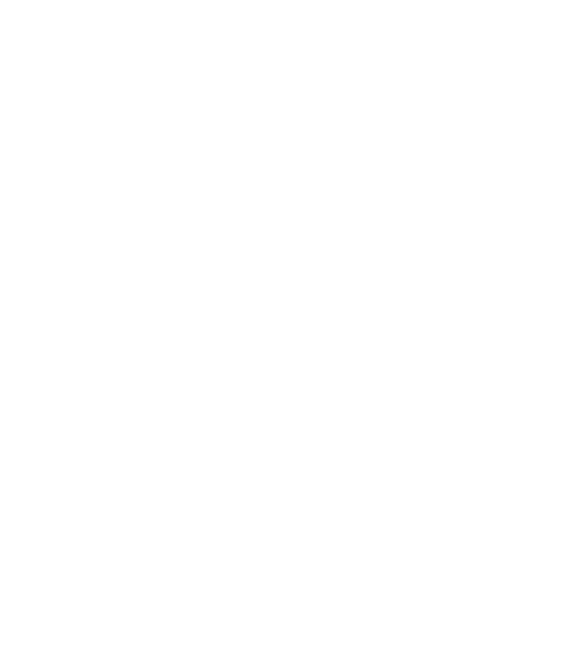