Quality Manager
Job
Overview
United States, Grover, North Carolina
- Engineering and Project Management
- Permanent
You are subscribed to our push notifications, but not currently for jobs like this.
Would you like to receive notifications for jobs like this as well?
Great news! You are subscribed to receive alerts for jobs similar to this one.
This vacancy has now expired. Please see similar roles below...
The Manager of Quality will develop, implement, and periodically evaluate a program to ensure the organization’s processes and business practices, from incoming materials to finished products, meet the quality, integrity, and efficiency standards set by the organization. The Manager will facilitate the deployment of a standard production system by developing and coordinating the implementation of Continuous Improvement System (CIS).
The Manager provides leadership of all Quality Control, which includes:
- Incoming quality. Secure incoming parts quality in collaboration with supplier quality and the logistics team
- Online quality. Responsible to capture data, analyze, implement containment and lead root cause analysis for online quality.
- Product validation. Responsible for the final quality inspection and product audit.
- Responsible to lead a team consisting of quality engineers, technician, & validation auditors.
Duties/Responsibilities:
- Evaluates production processes from a strategic level to ensure that products meet quality, integrity, functionality, and other specifications and requirements
- Directing all quality initiatives throughout the organization through oversight and management
- Responsible for managing, modernizing and implementing Quality and Safety tools, A3, 5S, Kaizen, etc.
- Maintain a constant drive for continuous improvement in all fields
- Contribute to the “lean thinking” education of all the employees and champion ‘lean thinking’ culture
- Deliver hands on coaching especially in problem solving. Map competence gaps and define training requirements to support all people in the journey
- Define, drive and follow up Quality activities. Make sure there is good prioritization and focus. Manage and coordinate the Quality KPI’s
- Maintain consistent and positive leadership, ensure team responsibilities are clearly defined and maintain a collaborative environment that promotes teamwork and growth opportunities
- Implement Continuous Improvement as the guiding principle for all employees & Activities
- Challenge the management and boost lean best practices within the organization to accelerate efficiency and to reach operational excellence throughout the organization
- Collaborates with management and senior staff across departments to draft and implement acceptable quality standards
- Develops and implements quality standard testing and evaluation processes
- Reviews quality control documentation such as checklists, logs, and reports for effectiveness, accuracy, and relevance
- Responsible for establishing processes that drive the business to process excellence and improve overall cost of poor quality while ensuring compliance with ISO9001, 14001 and OHSAS18001
- Periodically reports status of quality control to plant leadership and, when required, regulatory agencies
Education, Skills & Experience:
- Bachelor’s degree in engineering or related industrial field required; master’s degree preferred or equivalent combination of education, training, and work experience
- 10+ years in manufacturing management, preferably in assembly processes and/or related industry; or minimum of 15 years’ experience managing a significant segment of a large manufacturer or the entire processes of a smaller manufacturer
- Advanced training in Lean, PDCA, Kaizen, and other Continuous Improvement methodologies
- History of a process-oriented, flexible approach. Consistently delivering results on schedule in a fast-paced, dynamic environment
- Experience working with manufacturing-based technology, processes and principles is required
- Significant Lean deployment leadership experience in a manufacturing environment
- Comprehensive knowledge of quality systems, tools, and procedures required. Knowledge of ISO9001 & TS16949 preferred
- Advanced understanding of quality control standards and methodologies
- Thorough understanding of manufacturing and production in the automotive industry
- Good experience in change management and demonstrated ability to challenge an organization, whilst further developing an excellent working climate and atmosphere in alignment with the Code of Conduct.
TRS Staffing Solutions are an equal opportunities employer, and we welcome you to provide OFCCP data voluntarily here
We are an equal opportunity employer that recognizes the value of a diverse workforce. All qualified individuals will receive consideration for employment without regard to race, color, age, sex, sexual orientation, gender identity, religion, national origin, disability, veteran status, genetic information, or any other criteria protected by governing law.
Sign-up for Job Alerts
Our latest jobs
$ 23 Per Hour
United States, Anderson, South Carolina
Negotiable
United States, Grover, North Carolina
Negotiable
Spain, TARRAGONA, Tarragona
Negotiable
United States, Grover, North Carolina
Negotiable
United States, Newark, New Jersey
Negotiable
United States, Ridgeville, South Carolina
$ 120000 - $ 130000
United States, Ridgeville, South Carolina
Negotiable
Canada, Edmonton, Alberta
$ 85000 - $ 85000
United States, Ridgeville, South Carolina
Our insights
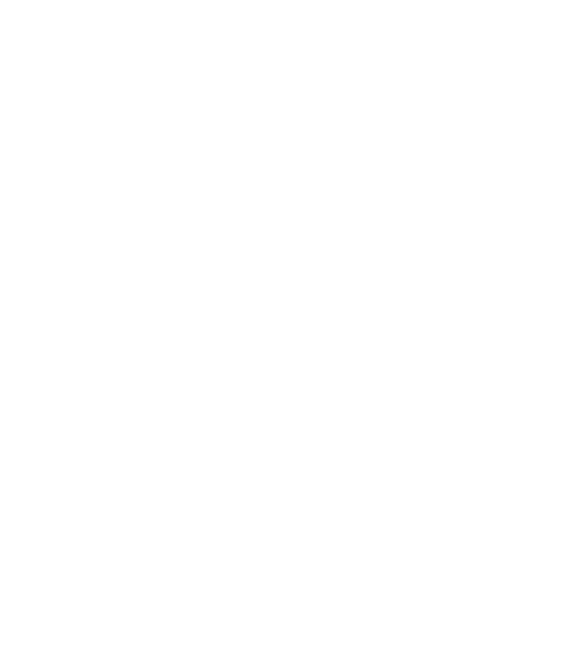